ニュース
ラティス・テクノロジーから発信する情報
お知らせ
SPECIAL 対談|大豊精機 × ラティス・テクノロジー
2021年5月12日
2021年
5月
点群モデル化へのパラダイムシフトで日本のモノづくりを
進化、深化、真価!
点群モデル化のソリューションを共同開発した大豊精機株式会社。同社は自動車部品や生産設備を事業の軸とする中で、現地現物と 3D モデルを融合した 3D デジタルツインの業務活用に積極的に取り組んでいます。
今回、岐阜県瑞浪市にある同社の 「技術開発センター」 で行った、大豊精機株式会社 代表取締役社長 真野 恭一様とラティス・テクノロジー株式会社 代表取締役社長 鳥谷 浩志との対談の様子をお届けいたします。
※当日は感染対策を徹底した中で対談を行いました。
大豊精機株式会社
設 立: 1973年5月9日
代表者: 代表取締役社長 真野 恭一
社員数: 463名(2021年1月時点)
事業所: 本社・本社工場 / 愛知県豊田市上原町折橋1-15 他
事 業: プレスの自動化装置およびその付属品の設計、製作、販売
省力化・環境設備、機械、器具、試作品の設計、製作、販売
プレス金型、ZAS 金型の設計、製作、販売。試作部品の製作、販売
自動車用量産部品の製造、販売(アクスルビーム・ロアアーム等)
ホームページ: http://www.tsk.taihonet.co.jp/
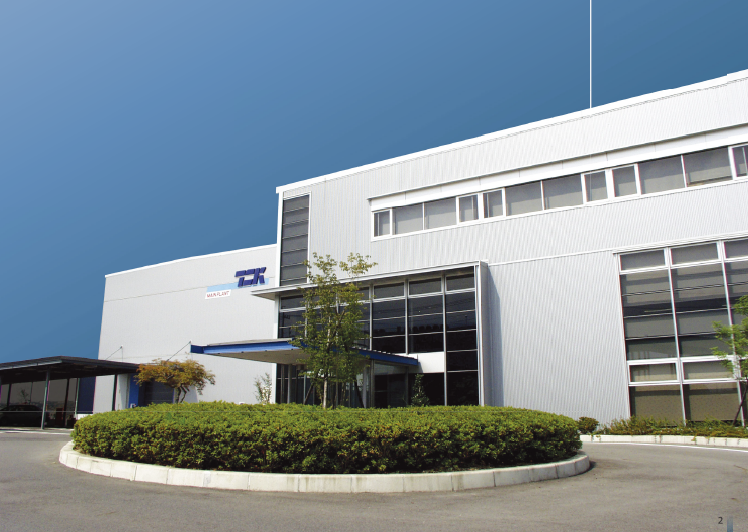
大豊精機株式会社 本社工場
大豊精機が考えるトータルエンジニアリング
真野:
本日は大豊精機の技術開発センターへご来社いただき、ありがとうございます。
(大豊精機株式会社 技術開発センター:http://www.tsk.taihonet.co.jp/development.html)
鳥谷:
お招きいただきありがとうございます。大豊精機さんとはラティスの XVL 技術を利用して、現地現物を点群モデル化して検証するソリューションを共同開発させていただきました。これは現地現物を CAD と同等のエンジニアリングデータに変えるという観点で画期的な技術だと考えています。この技術開発センターでその進化したデジタル技術体験させてもらえるということで楽しみに参りました。
大豊精機さんは自動車部品や生産設備を事業の軸とされていますが、モノづくり現場で時代の最先端をいくデジタル技術を活かされています。まず、その取り組みについてお聞かせください。
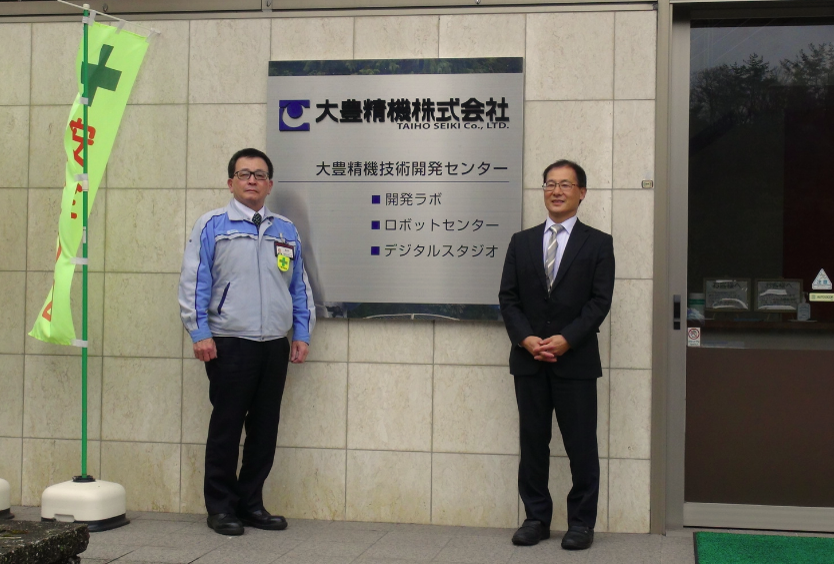
真野:
私共の事業を進める中でデジタルの活用は必須です。デジタル技術によるモノづくりの大改革の可能性と推進する難しさがありますが時代が進むにつれて、その必要性が加速されて、デジタル技術の有無がその会社の技術力のバロメーターともいえる時代になってきています。
モノづくりのベースとなる要素技術(弊社では塑性加工部品機能の開発~評価技術)、それと事業の軸を結ぶ技術(弊社ではロボティスク、設備技術)とそれを進化させるデジタル技術を融和させることが時代を生き抜くための活路と考えて取り組んでいます。
鳥谷:
モノづくりの技術とデジタル技術の融和という点がポイントですね。製造業・設備メーカーのデジタル技術の動向、課題とあるべき姿をどう考えてていますか。
真野:
大豊精機は今年で創業 48年となります。設備やモノづくりを軸に事業をしてきています。
弊社が基本とする考え方にトータルエンジニアリング(以下、TE と表記)があります。これは ”製品プロセススルー” という考え方と ”製造ラインスルー” の考え方でモノづくりをするものです。この 「TE」 を進めるには 「データ正」 の思想をベースにすることが重要です。特にこの大変革の時代、さらなる 「TE」 の進化・深化・真価がキーワードと 考えています。
技術進歩が加速する中で、製造業はグルーバル展開、新技術開発、コスト競争力はもとよりモノやコトの価値自体の変化への対応、要求される eSQCD(環境・安全・品質・コスト・デリバリー)も高い次元での両立が要求され、モノづくり環境は大きく変わってきています。
鳥谷:
消費エネルギー低減、ゼロエミッション、新技術やデジタル技術を用いた新たなモノづくりへの挑戦など山積する課題の中で、経験スキルやモノづくりを支えてきたベテラン層が減っているなど人材面でも厳しい状況です。製造業を直撃する難問ばかりですね。そこをどう乗り越えられようとしているのでしょうか。
真野:
おっしゃる通りで、これまでのやり方が通用しなくなってきています。
簡単な解決策はありませんが、シミュレーションのような事前検討をどれだけ丁寧に正しく実施できるか、経験やスキルの不足、新たな技術領域の指標に対して準備できるかが過去に増して重要になってきています。
事前検討、検証をやりきる為にはデジタル技術なしには不可能です。目指す姿は計画段階での完成度 100% ですが、まだまだ道半ばですが、今後も愚直に取り組んでいきます。
鳥谷:
それで大豊精機さんは各セグメントで CAE、FEM、シミュレーション、デジタル検討に力をいれて進めてきているのですね。
(CAE:コンピューター設計や構造解析、FEM:有限要素解析)
真野:
自動車部品でも生産設備でもモノづくりに関してはシミュレーションをしておかないとよいモノはつくれません。デジタル技術の貢献度が高いことが今後はさらに期待され、そこへの取り組みを怠ると時代に取り残されてしまうと考えます。
鳥谷:
先ほど、トータルエンジニアリングには 「データ正」 が重要と言われましたね。試作から量産、材料から完成品というトータルエンジニアリングを実現しようとすると 3D モデルを軸とする正のデータを活用したシミュレーションが重要になってきます。このシミュレーションでどのような課題を解決できるのでしょうか?
真野:
製造ラインスルーの例でお話しましょう。
例えば弊社が受注する設備は、新設工場に新設ラインを設置するだけでなく、稼働中の工場、生産ラインへ追加や一部変更、部分的な工程の入れ替え等々、いろいろな状況での対応が求められます。その様な多様性があるニーズに対して、現地情報をしっかり手の内にいれて仕様検討から設置据付、完成後の稼働状況までをスルーでシミュレーションすることが後戻りのない完成度の高い工場・生産ラインづくりに不可欠です。
過去には現地情報のモレや取得不足でしっかり検討出来ずに、作り直し、やり直しといった苦い経験もして、お客様にご迷惑をおかけしました。特に経験の少ない部分や新しい技術分野での新規製作は現地情報との整合性を重視すべきで、多くの関係者の意見を集約することは有効です。
鳥谷:
なるほど、その通りですが、現地工場、ライン全体の CAD データが整っている業界や分野はまだまだ少ないと聞いています。通常では関係者で現地現物のシミュレーション結果を共有することは容易ではありませんよね。そこで大豊精機さんの提案する 「現地データの点群モデル化によるデジタル活用」 が有効となるわけですね。
真野:
XVL フィールドで点群がモデルの様に扱えることで、現地スキャンデータの活用領域は格段に広がりました。
初期段階での全体のレイアウト検討では、工場全体を考慮したライン設置、コンセプトチェックが全員で可視化できました。生産部門や保全関係者、物流担当部署等々の面々が同じデータをもとに事前に工程を作りこみ出来るわけです。
データの見方、見せ方としては xR 技術の活用も極めて有効であり、誰もが検討実務そのものを実感、体感できて、意見や考えをその場でダイレクトに反映させながら進めるスタイルがこれからのデジタル技術の役目だと考えます。
鳥谷:
先ほど現場を現物大で確認する 「デジタル立ち合い、1分の1 検討」 と工場全体を俯瞰して見る 「点群ジオラマ」 を体験させていただきました。鳥の目と虫の目でライン全体を見る、なるほど全体を俯瞰して現地の詳細情報を洩らさず検証できるところは今までのレイアウト検討とは ”次元” が違いますね。
これまでの xR は CAD データありきでした。現地現物を点群モデル化することで構成の情報まで扱える、つまり CAD データと同等に扱え、検討内容の具体性・現実味が格段にあがっています。デジタルデータの存在しないものまで新しく xR で扱えるというのは革命的ですね。製作予定の CAD データや 2D データとの組み合わせも同一空間で確認でき、生産性、実作業のシミュレーションを事前に検討することもできる。検討段階の完成度向上を進める上で現地の点群モデルを活用するのは現地現物 DX の新しいアプローチといえますね。
真野:
体験してもらった点群ジオラマは全体を俯瞰しながら部分最適を全体最適のフィルターを通してチェックするのに有効だと考えています。私共もお客様の既存の工場、工程、設備や付帯までを全て網羅した構想提案が、今まで出来ていたようでしっかりとは出来ていませんでした。
現地現物を点群モデルを活用して新しいモノづくりのプロセスやシミュレーション結果を提案という形の、真の価値としてお客様に提供できればと思います。
アナログとデジタル、現地現物とバーチャルを結ぶ
鳥谷:
お客様の気づいていない検討やアイデアを一緒に引き出して提案を形にするというプロセス自体が新しい現地現物 DX といえますね。その提供する技術や手段は大きな付加価値をもっているとわかりました。このデジタル技術をビジネスとして展開を始められようとされていますが、まずどこから手を付けようとされているのでしょうか。
真野:
このデジタル技術を使って、これまでの仕事のプロセスをどのように変えるかを見える化し実感することが最初に取り組むことだと思います。
弊社も当初は実務での活用というところでは苦労しました。そこで、下の例のように現地工事への活用を図り、「デジタル RA(リスクアセスメント)」 の実施と工事手順の見える化と関係者での共有化が実現でき、安全の確保、工事期間の遵守(短縮化)、工事費用の低減などの効果が実感でき、一気に業務の中に展開できました。
最終的には、初期段階からモノづくり全体、そしてその後のサービスにまで渡って、各部門が一気通貫でデータを上手く共有化し活用できれば鳥谷社長の提唱される XVL パイプラインでのモノづくりにより一層近づけると考えています。
鳥谷:
日本の製造業を元気にできるツール、手法として点群データのモデル化は大いに期待できる予感がします。ここからの展開として点群モデル化はどう進めていくべきと考えますか。
真野:
IoT、DX、デジタルツイン等々のいろいろな言葉や考え方がありますが、モノづくりをする上ではリバースモデル(精密寸法)とモックアップモデル(ラフ寸法)は使い方を割り切って突き詰めていくべきと考えます。万能な手法は直ぐには構築できませんので、今ある手法で直ちに着手することで将来のデジタル化へつながると思います。
点群モデルで、皆さんのアナログとデジタル、現地現物とバーチャルを結び付ける役割をもって貢献したいと考えています。XVL フィールドで多くの人たち(業種、分野、役割を超えて)と利用拡大することで本当の意味での点群モデル化の効果が発揮されてモノづくりが変わると信じています。
鳥谷:
現地現物をスキャンしてひとかたまりのデータとして扱う点群データからエンジニアリングデータである点群モデルに変える。これは現地現物のパラダイムシフトです。近い将来、モノづくりの常識が大きく変化する可能性を秘めています。
真野:
その為にもまずは点群モデルを使ってもらう、良さを体験してもらえる様にビジネス展開を加速したいと考えています。
鳥谷:
今回、体験した点群モデルを活用した xR は現地現物 DX をイメージしてもらうには最適でしょう。日々現場で悩む他の製造業の方々にとって、ここを訪問することは、自分の仕事に当てはめるとどうなるのかを考えるまたとない機会になります。今のプロセスをこの手法でどう変革できるのか、最先端のデジタル技術で現地現物 DX はどう実現できるのか、たくさんの気付きが得られるでしょう。
ラティスとしても点群モデルやそれを組み込んだ xR を利用した XVL ソリューション群を進化させ、大豊さんとともに日本のモノづくり飛躍に貢献していく覚悟です。
真野:
ご期待に添える様、社内のメンバーと進めていきます。今後もラティスさんのご協力とご支援をお願いします。本日は、ご来社いただきましてありがとうございました。
鳥谷:
こちらこそ、大変貴重なデジタル体験をさせてもらいました。ラティスと大豊精機さんで連携してデジタル革新を起こしていきましょう。
END
・XVL はラティス・テクノロジー株式会社の登録商標です。
・その他記載されている会社名および製品名は各社の登録商標または商標です。
最新の XVL 関連情報をお届けする XVL メルマガを配信しています!
その他の SPECIAL 対談記事こちらから
点群モデル化へのパラダイムシフトで日本のモノづくりを進化、深化、真価!